Advice, support and technical documentation
Beyond the design and the manufacturing of high power LED illumination, TPL Vision’s mission also consists of bringing advice and information to its customers, about
- selecting a new lighting solution,
- or using existing solutions.
Thanks to their experience in the LED illumination field, TPL Vision’s engineers are always receptive to lighting issues for machine vision systems, from the simplest to the most complicated. They are committed to offer individualised advice and help customers find the best solution for every project. Whatever the kind of application, they know which features are essential to consider (kind of workpieces, camera model, available space, environment, etc.) before expressing any recommendation.
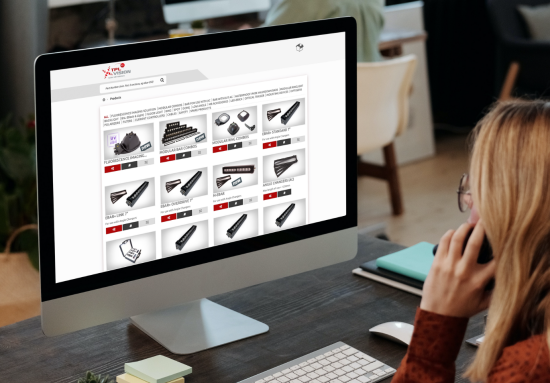
Frequently Asked Questions
TPL Vision encourages customers to strobe our LED products whenever possible, as it reduces the heat generated within the product and increases the lifetime of the LED chip. Operating TPL Vision products in strobe mode wherever possible can help extend product lifetimes.
Most TPL Vision products (with the exception of UV and “Expert” products) come with a 3 year warranty and rated lifetime of 50,000 hours when operated in continuous mode with ambient air temperature = maximum 40°C. This lifetime can typically be increased using strobe mode where possible.
LEDs are chips enclosed within a casing, together with a preliminary optic. When any LED is turned on, it produces a high amount of heat which is detrimental to the lifetime and performance of the LED. TPL Vision’s LED products are mounted on a metal surface (heatsink) to conduct the heat away from the LED and give the best LED lifetime possible.
However, it is impossible to fully extract all the heat generated from the LED, and heat degradation will gradually reduce the power of the LED over its lifetime. This is a normal characteristic of LEDs, and all LED chips will experience a reduction in power output as they age. Operating products in strobe mode can help extend product lifetimes.
Duty cycle is usually used in conjunction with discussions on overdrive operation of a light as it describes the relationship between the “on” period and “off” period within the repetative cycle of turning a LED on and off. Duty cycle is commonly expressed as a percentage or a ratio of these two periods. When operating a light in Overdrive mode you must respect the specified maximum duty cycle for the switching of the light on and off so as not to damage the light. TPL Vision has some products, such as the M-EBAR, with an “on-board” safety control to ensure that you do not switch the LED’s on for an excessive duration to avoid damage.
An ‘expert’ product in TPL Vision’s portfolio is an illumination product that has no current control within it. The products must be controlled via an external current controller. This means the customer is left to drive the LEDs with as much current as they want. However, a customer who uses the product in this way must be careful to protect the LEDs to ensure the maximum lifetime. If the customer does not follow the recommended maximum current and respective duty cycle recommendations they can risk damaging the LEDs by letting the junction temperature in the LED get too hot.
Colour Temperature of an LED is only applicable to white LED’s and it describes how cool (blue) or warm (red) a particular white light source looks. Colour Temperature is important when you are needing to have a true or faithful colour image captured. The Colour Temperature Spectrum is from 1000K to 10,000K. TPL Vision selects LED’s that are in the “neutral”, central range of this spectrum – it will vary between products but the colour temperature is typically between 5,500K to 6,500K. Alternatively this can be thought of as approximately equivalent to Daytime Sunlight and Daytime Cloudy conditions respectively.
Due to the extremely sensitive process of manufacturing an LED chip, all LED manufacturers test the wavelength/colour and brightness characteristics of every LED chip produced, using a special machine. This machine measures the LED’s characteristics and puts them into one of several “bins”. Each bin will contain LEDs within one tightly controlled brightness and wavelength group. All the LEDs look the same, but the characteristics of the illumination will vary slightly between each bin.
TPL Vision closely monitors the binning of the LEDs we purchase to ensure the quality and consistency of our products, and to ensure you don’t experience variations in LED colour or brightness on any one product, or product batch.
- Only two or three bins which are extremely close in characteristics are used within one product range, and
- the bins used on any one product purchase order will always be the same.
It is important to note that if the illumination is a repeat order, the binning may be slightly different between the orders, so there could be a small variation in colour or brightness. Typically, this will not be visible to the vision camera. However, the human eye is very sensitive to colour variations, so it is possible that users can experience a small difference in colour. This variation is very unlikely to affect the performance of a vision system.
Please note that TPL Vision products cannot be rejected for variations in binning, so if your application requires a particularly tight control on wavelength and/or brightness (especially for repeat orders), please discuss this with your Sales Executive prior to ordering.
IP ratings indicate how effective electrical enclosures are at blocking foreign bodies such as dust, moisture, and liquids. TPL Vision’s products are tested according to the IEC 60529 standard, which rates the product enclosures’ protection against ingress of solid particles/objects and water. It is commonly specified by the end customer which IP rating is required for their factory or machine.
IP Ratings Explained
Almost all TPL Vision products have an enclosure around the electrical components. These enclosures are tested according to the standard IEC 60529, which clearly defines Ingress Protection (IP) ratings using a code. The code rates the product enclosures for their protection against ingress of both solid particles/objects (see X below) and liquids, specifically water (see Y below).
IPXY Code descriptions:
- 1. Protection from the ingress of large objects greater than 50mm in diameter e.g. a hand.
- 2. Protection against fingers or other objects greater than 80mm in length and 12mm in diameter.
- 3. Protection from entry by tools, etc, with a diameter of 2.5mm or more.
- 4. Protection against solid bodies larger than 1mm (e.g. fine tools).
- 5. Protection against dust that may harm equipment.
- 6. Protection from all ingress of dust (dust tight).
Source: IEC 60529
* Note: 0 (eg in IP 40) means no protection.
- 1. Protection from condensation.
- 2. Protection against water droplets deflected up to 15° from vertical.
- 3. Protected against spray up to 60° from vertical.
- 4. Protected from water spray from all directions.
- 5. Protection against low-pressure water jets (all directions).
- 6. Protection against strong water jets and waves.
- 7. Protected against temporary immersion – 15cm to 100cm for 1 minute.
- 8. Protected against prolonged effects of immersion under pressure.
- 9K. Protected against close-range high pressure, high temperature spray downs.
All new products from TPL Vision are rated to IP65 as standard – providing dust tight protection and low-pressure water jet protection. Some older products do have a lower rating, so it is important to consider this when choosing your illumination product. Importantly, ingress protection does not mean the product can be exposed to oils and lubricants as the properties are different from water. Oils, lubricants and other non-water liquid substances are not covered under warranty unless otherwise stated in the product datasheet.
Please ask your TPL Vision Sales Executive for assistance if required.
Tech Notes - Machine Vision Lighting Techniques, Industry Terms and More...
Insufficient lighting is a main cause of failures when it comes to building reliable and robust vision systems. We have collected a range of resources about machine vision lighting techniques and applications to help you understand the role of illumination as well as our own processes at TPL Vision.